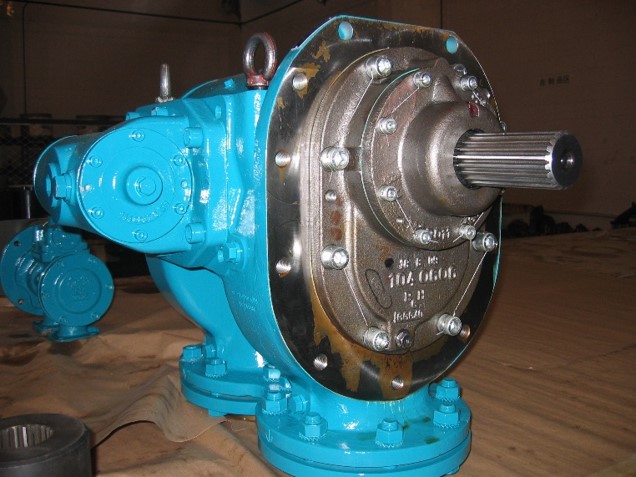
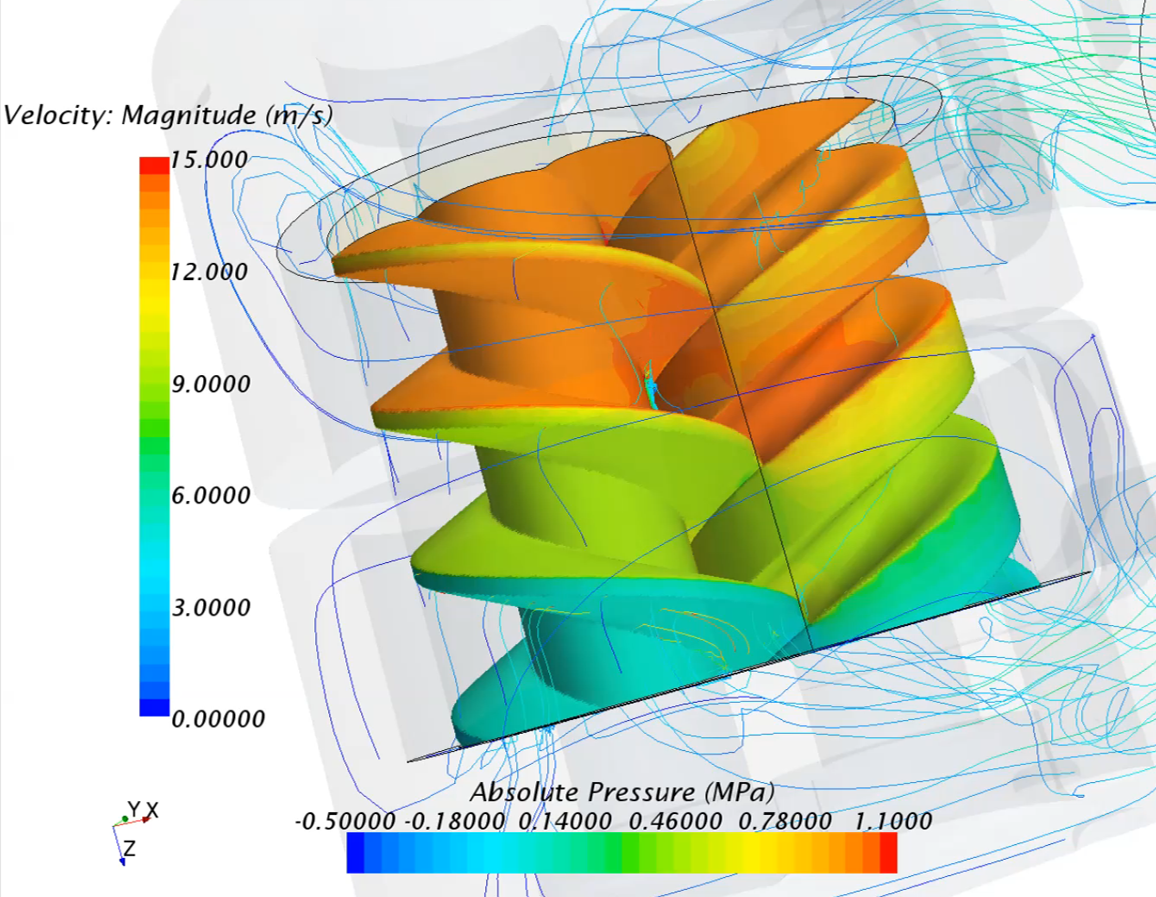
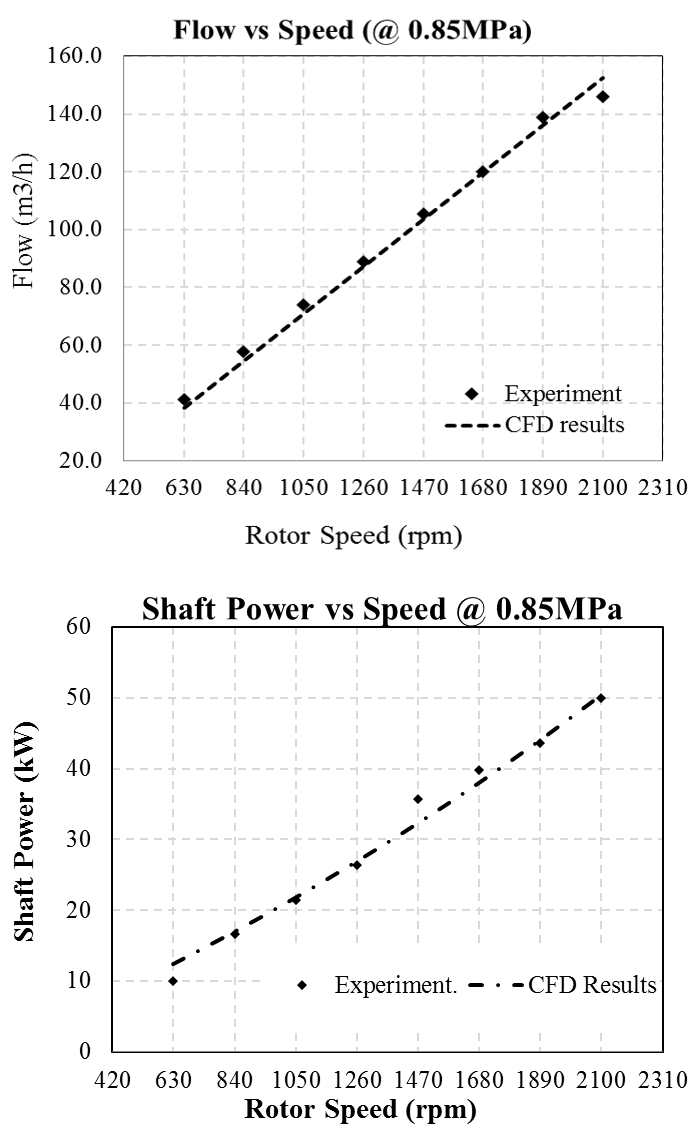
Numerical investigation of twin-screw pump by use of CFD
Grid generation: SCORG
CFD Simulation: Star CCM+
Increasing demands for high-performance screw pumps in oil and gas and other applications require a deep understanding of the fluid flow field inside the machine. Unfortunately, some important influence factors on the performance are difficult to observe by experiments. However, it is possible to study such effects using well-validated computational fluid dynamics (CFD) models.
The structured numerical mesh consisting of a single computational domain for moving screw pump rotors allows 3D CFD simulation of such machines. The mesh is generated by the unique grid generation software SCORG.
It was integrated with the commercial CFD solver STAR-CCM+ by user-defined functions (UDF) to manipulate predefined numerical grids to obtain pressure and velocity fields within the machine. This allowed calculation of instantaneous mass flow rates, rotor torque, local pressure field, velocity field and other performance indicators, including the indicated power.
A calculation model for the bearing friction losses was introduced to account for mechanical losses. Different turbulence models were applied and compared.
The CFD model was validated by comparing the numerical results with experimental data. Validation includes comparing mass flow rates, shaft power, and efficiency under various speeds and discharge pressure. It has been found that the predicted results match well with the measurements. The results showed that an increase in viscosity increases the mass flow rate and higher volumetric efficiency. It also leads to increased rotor torque and power consumption at the same time.
The analysis presented in this paper contributes to a better understanding of the working process inside the screw pump. It offers an excellent reference to improve the design and optimise such machines. In the future, this model will be used to analyse cavitating flows and determine the performance of other multiphase screw pumps.
Full paper: Numerical modelling of twin-screw pumps based on computational fluid dynamics
For more details, please contact us.